Processing & Treatment Services
Chevron Glass can provide a wide range of processing and treatment services which includes the following:
- Arrissed Edge
- Flat Polished Edge
- Flat Smooth (Ground) Edge
- Mitred Edge
- Tipped Corners
- Radius Corners
- Finger Grips
- Notches
- Cut Outs
- Holes
- Toughening
- Heat Soaking
- Heat Strengthening
- Shape Cutting
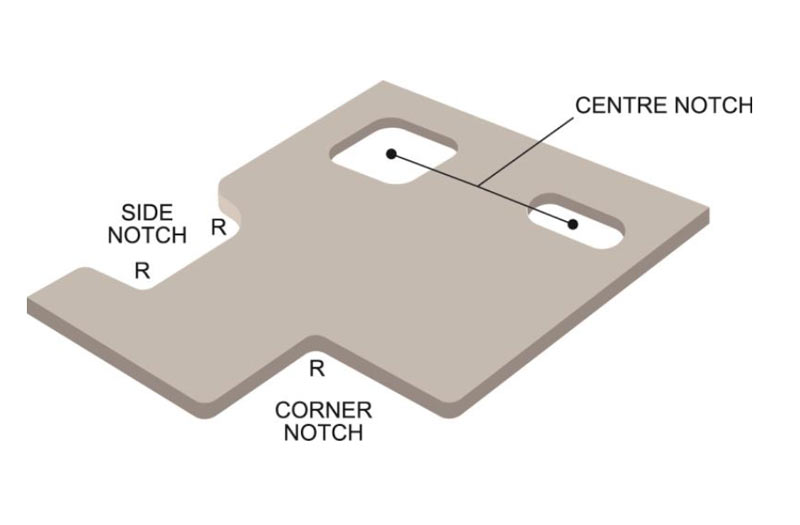
For a full list of our processing and treatment services with definitions and specifications, please download our specifications sheet.